In this step-by-step guide, we'll walk through the process of creating media profiles(*PMMs) tailored for DTG printing. Whether you're a seasoned printer or a newcomer, understanding how to optimize media profiles is crucial for achieving vibrant and accurate prints all whilst minimizing the amount of ink used. This approach to DTG is consistent with our promise to users to maximize profits without compromising on quality. Additionally, we'll delve into the Editor DTG separation tool, exploring its features and demonstrating how it integrates with your previously created media profiles.
Creating a DTG PMM
Creating a PMM tailored to a DTG workflow is very similar to creating a regular PMM as explained in our
Creating a PMM how-to video with a few important differences. In this example we're using a Kornit Atlas Max with CMYKRG inkset, although the steps seen in this article are the same for other DTG devices and inksets. It is advised to watch the
Creating a PMM video first so that you understand the basic concept of the PMM wizard and where to find it. So let's get started..
Important Notes:
- It is best practice to build a separate profile for each different colored garment.
- The linearization of the White and subsequent brightness adjustments will be very different depending on the lightness of the garment.
- The two linearization charts (white and color) should be measured in for DTG systems using the “Average 3x” setting. Otherwise, there could be significant bumps in the resulting curves and high DeltaE reported after measuring the Full Gamut.
Start a new PMM on your DTG printer, configure the print mode settings & proceed to give it a name:
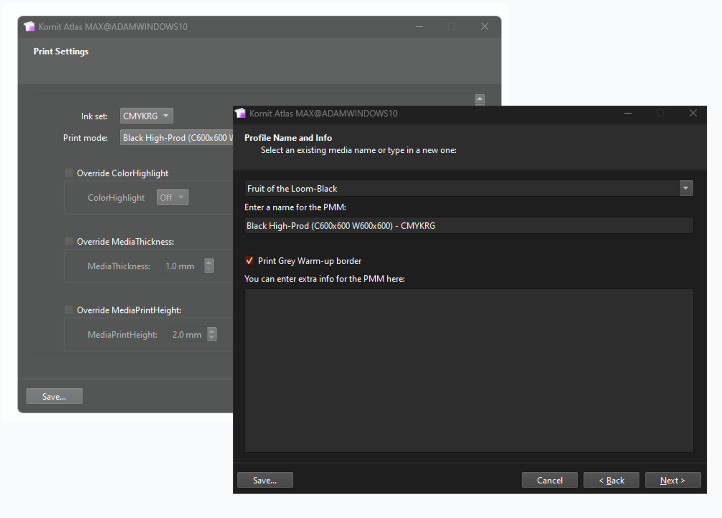
After clicking next you will find yourself on the White linearization page, you will need to print the linearization chart to make the first visual assessment. At the bottom of the linearization chart you will see this interesting yet important feature:

This feature added to the White linearization chart is designed to assist in determining the maximum allowable amount of White ink for printing on a garment without encountering negative overinking effects. The top bar of the chart illustrates 100% White ink coverage across the entire width. The bar beneath it starts at a 5% White block on the left and progressively increases in 5% increments until reaching 100% White. The bottom bar features White 'teeth' that mirror the ink percentage of the block above. Overinking effects, such as cracking in solid ink blocks and spidering in the teeth, should be monitored. The following example showcases White spidering in the teeth, with an arrow indicating the point to clip the White ink. In this specific case, the White ink was clipped at 75%, as exceeding this threshold resulted in overinking defects in the teeth as seen in the close up photo on the right:
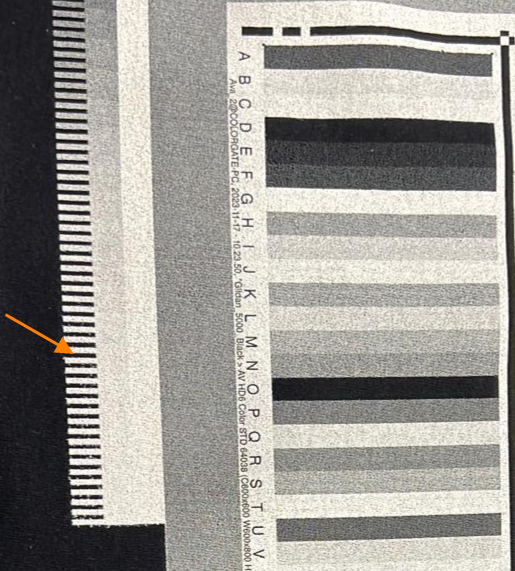
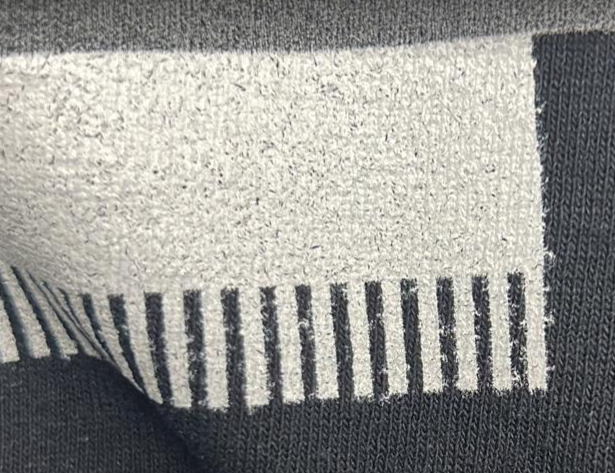
After you have made a visual assessment of the maximum White ink limit (some printers are perfectly capable of being left on 100%) then you need to return to the White linearization page and set your chosen maximum ink limit & print the chart again:
After measuring the chart, click the Next button to proceed to the next step:
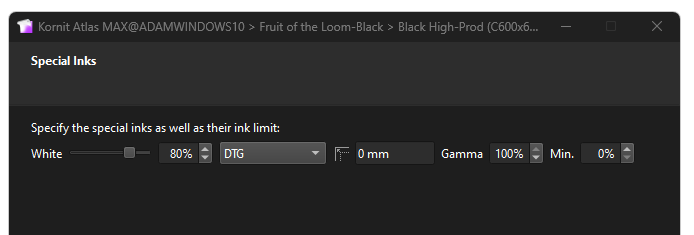
DTG is already selected in the drop down menu, therefore you can click Next again without making any changes and proceed to the next step.
Now, we get to the DTG Brightness and Ink limit chart, a crucial step in determining the White ink underbase percentage applicable to colored components within your DTG image. This chart shows a combination of different inks, the more colors in the inkset the higher the number of combinations required to measure. The printing and measuring of this chart constitutes 90% of the process, providing foundational data. The remaining 10% involves a visual assessment, serving to confirm or fine-tune the constraints established by the measurements:

In the above screenshot, the DTG Brightness chart is showcased on a black t-shirt, revealing the wizard's automatic removal of the White underbase in areas where there is 100% Black. This elimination is a result of utilizing the black of the t-shirt, eliminating the need for a White underbase. Additionally, the wizard has made adjustments to the White percentages in other color combinations, according to the measurements. It is essential to visually inspect the chart and customize the percentages if required, especially in response to undesirable overinking effects, paying close attention to the darker colors.
The next step is the color linearization which will have the White underbase applied underneath. You simply need to print & measure this chart & go to the next step showing you the spider chart:
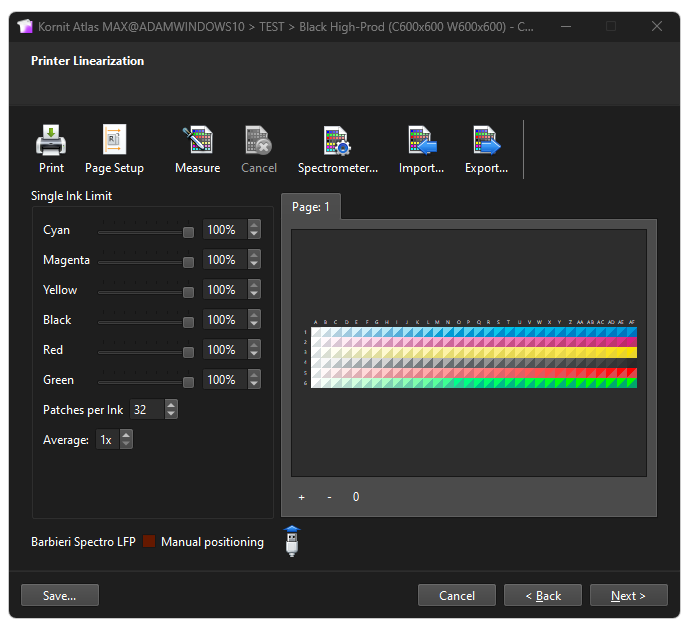
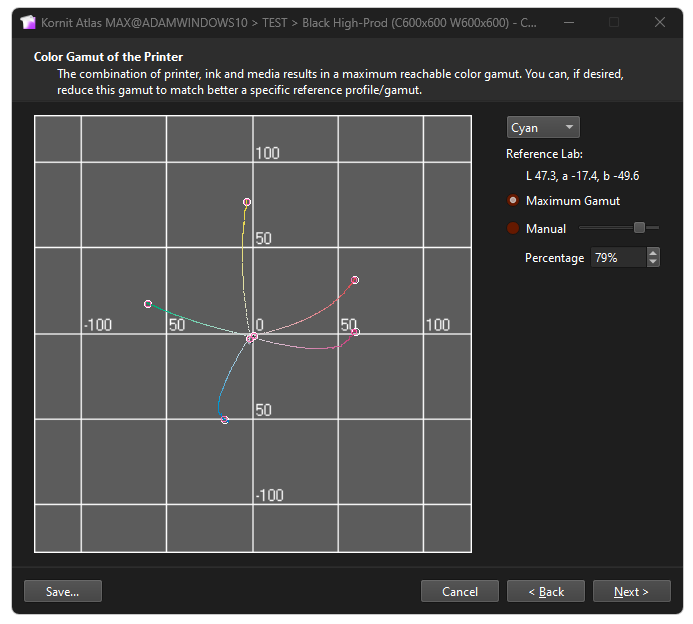
In the spider chart above, if the ink percentages are very close to 100% you can manually drag the slider to 100%, if not you can leave it at the predetermined amount based on the previous measurements. Proceed to the Total Ink limit chart:
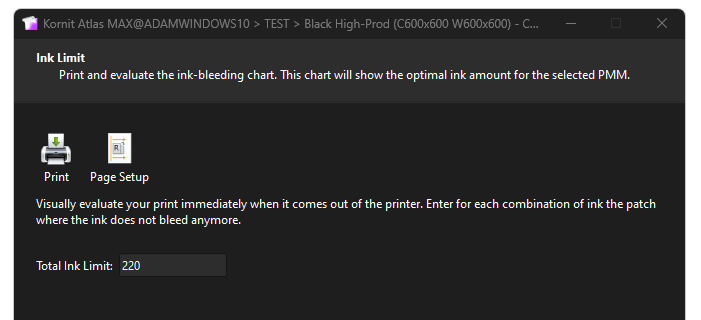
The Total ink limit will be automatically decided based on the previous measurements. In DTG it is less important to print this chart, in most cases you can trust the automatic ink limit and proceed to the next step. Having said that there is also no harm in printing the TAC chart if you would like to confirm the automatic TAC choice.
Next is the color gamut chart, it simply needs to be printed & measured serving as the final stage in completing the profile:
Important Notes:
- It is best practice to build a separate profile for each different colored garment.
- The linearization of the White and subsequent brightness adjustments will be very different depending on the lightness of the garment.
- The two linearization charts (white and color) should be measured in for DTG systems using the “Average 3x” setting. Otherwise, there could be significant bumps in the resulting curves and high DeltaE reported after measuring the Full Gamut.